June 2022 Issue Index
Safety by elimination
Accurate, timely data around conformance to design eliminates problems before they escalate and dramatically improves operational safety and productivity.
Accurate, timely data around conformance to design eliminates problems before they escalate and dramatically improves operational safety and productivity.
Transforming the volume of data collected on a site into timely decision support information presents a challenge. It is not sufficient to complete mine design compliance checks after excavation has finished. Understanding what went wrong after the fact does not resolve issues. Feedback about design compliance must happen during excavation.
Maptek conformance solutions are based on comparing detailed point cloud information captured daily against the short term design. Multiple sections can be created from one scan to precisely define how an as-built wall, bench or drive matches a particular design.
One key advantage of the laser scanning approach is the ability to measure and compare active mining faces from a distance. Reviewing critical data in the field allows teams to act safely and efficiently to keep mining on track.
All underground and open pit mines, including quarry and dredging operations can use Maptek design conformance tools.
Short term design requires constant refining on a daily basis. Timely conformance reporting has implications for key design decisions on parameters like depth to floor or wall angle.
Feedback available at the stages where it can have a positive impact on the quality of the design delivers maximum benefit to the design process.
Design conformance creates a robust quality feedback loop around one of the critical production processes in a mine. It reduces variance and provides timely, accurate information about conformance to design along production quality principles.
When functional stakeholders and management can quantify material variability at each stage, confidence is boosted in the business proposition.
Business costs associated with implementing digital conformance systems are relatively low. Workflow processes do not change significantly for stakeholders. Only the tool being used to guide a process changes, offering a result that is much faster and easier, more accessible and accurate.
Planning assumptions are improved by monitoring and optimising the modelling, design and execution of a mine plan. It is no longer necessary to delay milestone reporting. Maptek provides the technology to make this achievable for day to day operational improvement.
Work safely in the field
Design conformance on the Maptek FieldHHC supports production goals through an intuitive field process that delivers immediate and accurate conformance data, allowing staff to make informed decisions in the field. Conducting in-field conformance directly from laser scans allows operations to:
- Actively monitor conformance without interrupting production
- Increase highwall and bench safety, with improved wall stability
- Resolve issues quickly without waiting for in-office processing
Work confidently in the office
Streamlined, easy-to-use reporting tools help ensure that decisions are based on the latest data and drive improved resource recovery. Panoramic scene creation provides instant visual confirmation of conformance to design. Reporting from a single source of data promotes confidence in decisions:
- Improved communication between engineers, surveyors, supervisors and operators
- Timely feedback of useful information to other teams
- Evaluation of mine performance and improved resource recovery
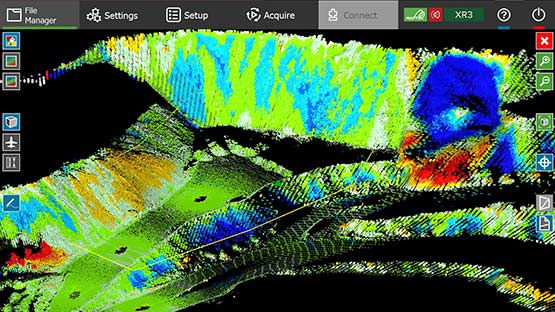
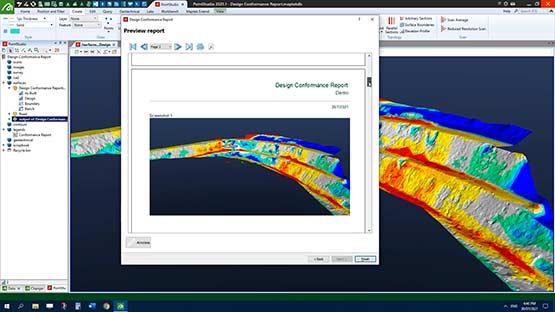
Work where you are with the tools you need and experience the benefits
Design conformance
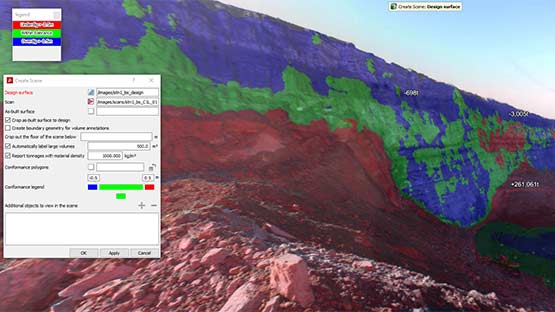
Decision support – Accurate, reliable data supports confident decision making across geology, geotechnical and mine planning teams
Streamlined workflow – Built-in workflows, advanced analysis and easily customisable reporting
Safety – Meet operational KPIs for increased safety and risk management through comparing designs to digging
Inter-ramp compliance
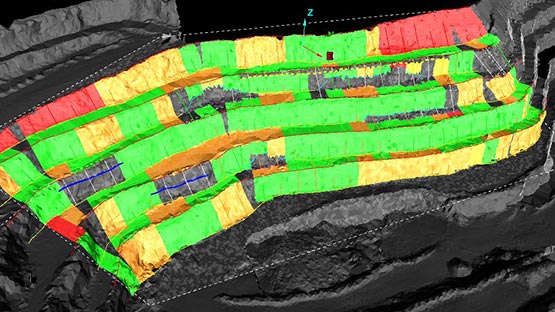
Decision support – Data to support daily digging requirements for pit supervisors or open cut examiners
Compliance – Engineering studies comparing as-built to design and ongoing compliance
Safety – Geotechnical monitoring helps minimise risk to people and machinery
Haul Road Tools
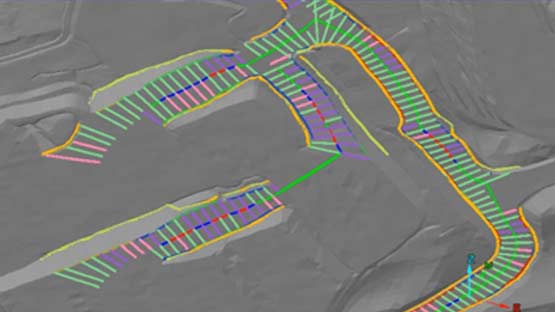
Decision support – Easily identify non-conformant areas for quick resolution
Flexibility – Apply to as-built surfaces and design models
Efficiency – Minimise operational costs and improve productivity
Safety – Better road designs lead to safer operations
Underground reporting
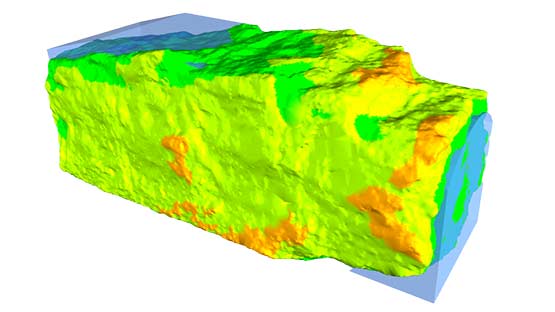
Decision-support – Quickly generate customisable reports for confident decision making
Multiple applications – Minimise grade dilution, highlight unstable areas and analyse shotcrete thickness to reduce development costs
Safety – Apply to development drives, stopes or crosscuts to quickly identify areas requiring attention
-
Streamlined, easy-to-use reporting tools help ensure timely, accurate data for decisions across geology, geotechnical and mine planning
-
Laser scan technology enables operations to safely measure and compare active mining faces in the field for conformance to design
-
Visual communication is a hallmark of Maptek in-field and office applications, supporting advanced analysis and customisable reporting