March 2020 Issue Index
Innovative charge design
Maptek BlastLogic provides a tailored workflow that allows operations to quickly recalculate charge rules based on pit observations.
Maptek BlastLogic drill and blast design and reconciliation solution provides a workflow that allows operations to recalculate charge rules based on pit observations. Connecting blast designs with changing pit conditions enhances mine safety and productivity.
Crew members are the eyes and ears of the drill and blast engineer in the field. Engineers use the information crews provide to create and update practical, achievable plans for them to carry out.
In the absence of digital modes of sharing information, paper maps are sometimes used. Frequently, engineers rely on verbal communication that can be subject to misinterpretation and leaves no audit trail. At times charge designs are created based only on the modelled information, excluding field observations.
Without Maptek BlastLogic, any variance or change in pit conditions (such as wet holes or signs of a reactive material) requires crew members to wait until new paper-based charge plans are issued and sent to the pit. With up to 10 changes commonly required per shift, an average crew can lose several hours of productivity per week.
The BlastLogic digital workflow is helping customers reduce downtime and reap the benefits of a data-driven decision-making approach.
Geotechnical engineers, geologists and shotfirers use the BlastLogic Tablet for digital capture of hole-by-hole field observations. Combining these expert mine observations with the latest QA/QC and drilling data, BlastLogic automatically recalculates the required charge amount.
This recalculation is done on the bench while the tablet is online or offline regardless of network connectivity. Crew members are not required to travel to the engineering team to receive the new charge plans. This can save an hour or more in downtime whenever conditions change.
Most sites have geotechnical and geology teams that inspect the drill cuttings post drilling and correlate real-world observations against the modelled information. Any differences between actual and modelled information inform decision making.
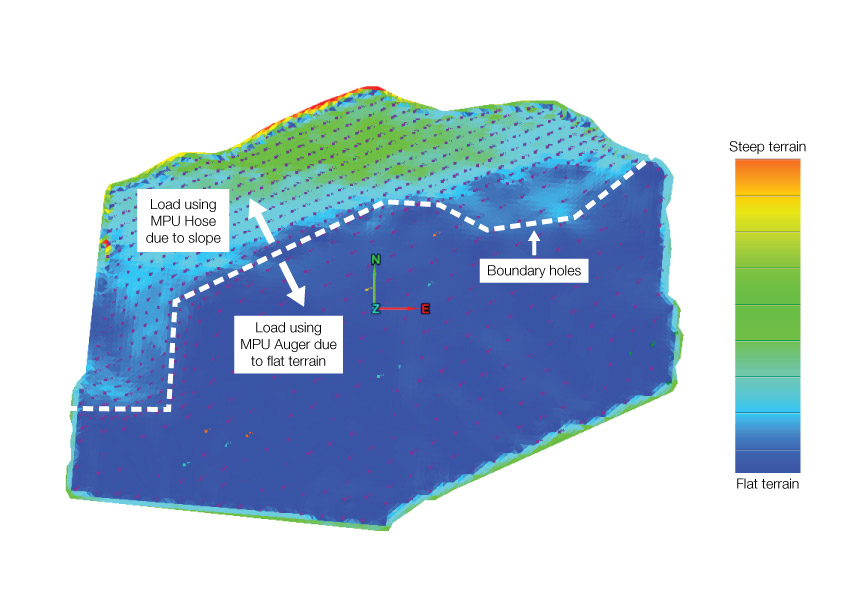
Information lost due to paper-based communication can lead to major safety and cost risk. BlastLogic has broken down communication silos between different groups and enabled an integrated digital approach that produces safe and productive drill and blast outcomes.
BlastLogic allows effective digital capture of such information, using the tablets for blast reconciliation.
All information is stored in a central server and can be directly fed to automated reports or charge plans. For example, BlastLogic can be configured to allow mine geologists to note the presence of reactive material per hole. The charge plans will be automatically recalculated and show the planned explosive product under reactive conditions.
Similarly, geotechnical engineers can capture fault or shale information per hole. The tablet charge plan is automatically triggered to recalculate and show no or reduced charge.
Automatic recalculation has solved another common issue for mine sites, where the loading mechanism is chosen based on blast crew field observations. Areas with steep slopes typically require blast crews to drag the explosives hose from the trucks or Mobile Processing Units (MPU). Sections with flat terrain can be loaded using the MPU auger and generally result in less manual handling of the hose.
As shown in Figure 1, drill and blast engineers can generally approximate the loading requirements using BlastLogic in the site office. However, this depends on the accuracy of the survey data and actual ground conditions.
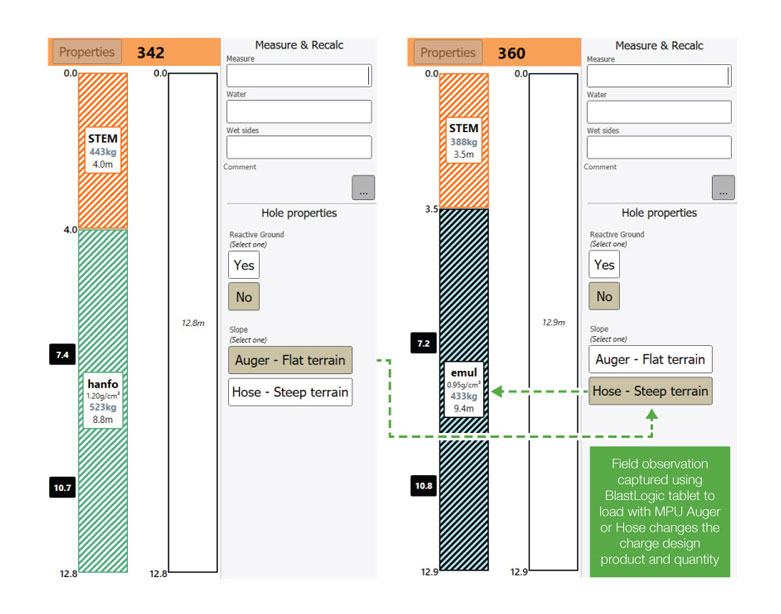
Most mine sites rely on the blast crew in the pit to make a final decision whether to use auger or hose, based on personnel and equipment safety. This fundamental requirement to change charge plans often leads to crew members manually calculating the charge amounts, since the hose and auger loaded explosive products have different densities.
Occasionally, areas where the maximum explosive amount per hole is capped due to vibration require the crew to wait until new charge plans are issued by the drill and blast engineers with another round of vibration checks.
BlastLogic recalculates the required charge amount based on blast crew observations, as shown in Figure 2. This allows conformance to vibration limits and avoids manual calculations or potential miscommunication. All this with the click of a button!
Whether an observation recorded on the BlastLogic tablet leads to an automatic change in charge plans is ultimately a site decision.
The digital data flow supports engineers to respond appropriately to the need for changes in real time, knowing that the decisions are founded on actual pit conditions.
Consideration of practical constraints and a user-friendly and stable interface makes BlastLogic a global leader in blast innovation.
- Recalculating charge rules based on pit conditions enhances mine safety and productivity.
- BlastLogic breaks down communication silos between engineers and blast crews in the pit.
- Digital data flow supports decisions in drill & blast in response to changing real-world conditions.