June 2018 Issue Index
Integrated production reconciliation
MinLog developed a unique MineSuite configuration, providing a single system which integrates with third-party systems for accurate, timely grade reconciliation.
A well-known coal supplier in Australia uses one of the world’s largest mining service providers for contract mining. The contract is based on production gains or losses when comparing geologically defined reconciliation areas against product delivered.
To optimise gains, the contractor decided to build a pre-treatment plant (PTP) to beneficiate material that would normally have been treated as waste. A means to measure the efficacy of the PTP was then needed.
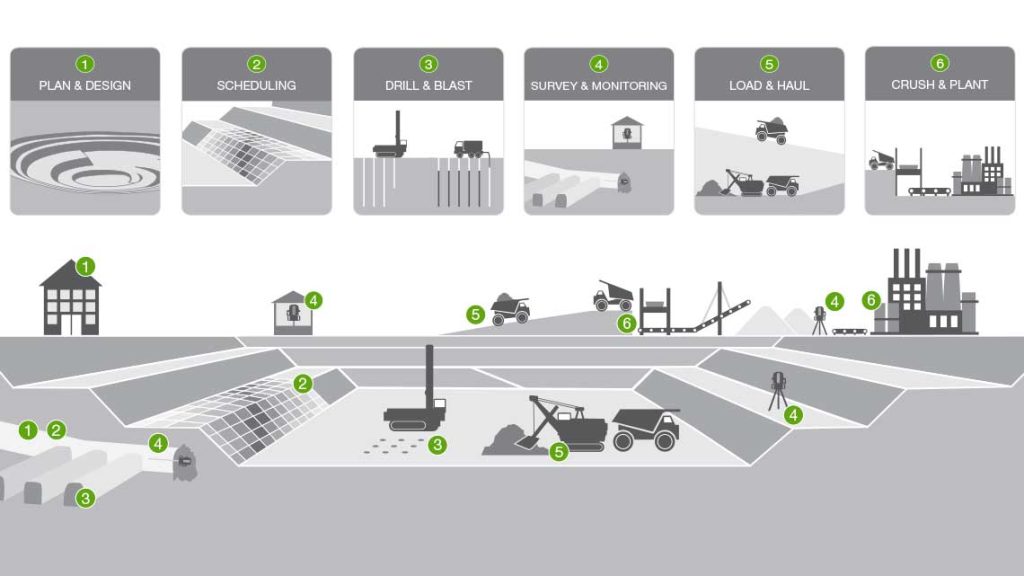
The contractor recognised the value of a single system to integrate with third-party systems in order to provide accurate, timely grade reconciliation.
Gains and losses are calculated by referencing the geological block model used by the mine owner.
The contractor’s challenge is to determine deficiencies in their mining method or discrepancies in the geological block model.
The contractor uses a range of Maptek solutions, including Vulcan, BlastLogic, I-Site and Eureka to measure the exposed ore and determine mining competency.
A means of integrating the Maptek data with fleet management and client-owned coal handling processing plant (CHPP) information is required for accurate calculations. The contractor also wanted to determine gains due to the PTP. A MineSuite configuration achieved this objective.
MineSuite MineReconciler and PlantManager will allow geologists to integrate information from Maptek and other third-party systems. This information will be contextualised in the MineReconciler, allowing geologists to validate, correct and approve values emanating from the various source systems and associated with specific geological reconciliation areas.
MineSuite Reports will be used to view contractual results and identify specific opportunities for improvement. The effect of these improvements can then be measured and reported on.
Modelling processes
Activities, functions and processes are modelled in the MineSuite Process Model to measure KPIs. This includes the geological and mining business units and the PTP modules and equipment. The PTP model is hierarchical from high level processes down to individual equipment.
Stockpiles have also been identified and modelled as part of the MineSuite process flow. Stockpiles and material on them are associated directly with the source geological reconciliation area. Material can be tracked throughout the process, enabling reconciliation with the geological block model.
Measuring processes
Measuring material movements from source to destination is critical in determining mining performance.
Mined material is measured, processed and moved by various operations such as geological modelling, drill and blast, and load and haul.
Each of these operations has an inherent level of accuracy and importance to the overall efficiency of the mine. All information needs to be recorded and reported on, to allow individual operations and the combined mining system to be understood.
Typical operations in this material movement chain include:
- Geological block models (such as those from Vulcan)
- Drill and blast results (such as those from BlastLogic)
- Load and haul movements (such as those from MineSuite FMS or other systems)
- Supervisory control and data acquisition systems (as used in CHPP systems)
- Laboratory information management systems
MineSuite solution
Most mining operations have at least some existing or automated data which can be fed into MineSuite to avoid the resourcing and accuracy issues with manual or duplicated data capture.
Automatically generated data is uploaded into MineSuite via specific services and may be corrected and validated. MineSuite also provides for manual data entry and validation via the MineReconciler and Electronic Log Sheet.
The data is contextualised and validated, and can be presented in several ways. In MinLog’s experience, whether automatically or manually captured, data may be invalid or erroneous and unsuitable for presentation. MineSuite MineReconciler gives engineers and geologists powerful tools to quickly correct, validate and approve data.
Different dimension formats are mapped for reuse throughout the module and reconciled back to the original geological block model.
This ensures that the results of each step in the mining value chain can be quickly and effectively measured and analysed in context, eliminating repetitive tasks.
MinLog configured and developed a unique solution to the specific challenges of this implementation. MineSuite has proved to be an adaptable system for collecting and managing data across an operation.
Accurate and timely information is an essential key to improving productivity, and MineSuite solutions can transform your mine.