March 2021 Issue Index
Measuring plan conformance
Maptek has tailored an automated approach to measuring mine compliance that allows engineers more time to analyse results and make timely decisions.
The Maptek mine compliance concept measures how closely a mine budget is being adhered to. Lack of plan conformance can be critical to business success.
Budget deviations can be costly, with unplanned work being 1.5 to 5 times more expensive than planned work. Mill blend non-compliance results in recovery issues and the need to account for unplanned blending. Value is lost when an optimised plan is not able to be followed through.
Non-compliance is a risk that mines must attempt to prevent, control and mitigate. When mining deviates from plan, timely intervention is crucial. Information must be available where and when it can make a difference.
An automated solution enables timely analysis and fast response to correct deviations and improve adherence to the mine plan.
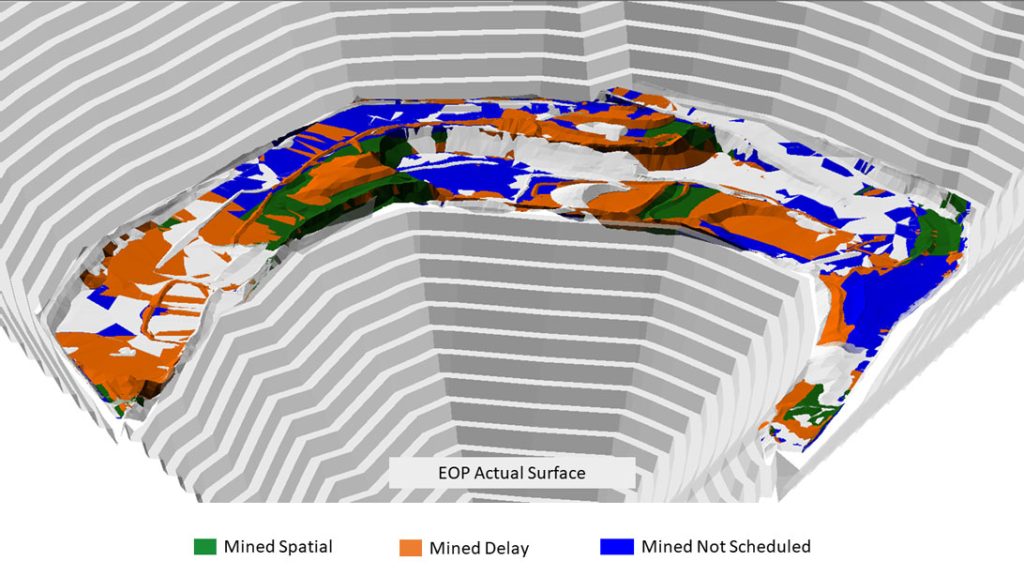
The Maptek approach includes automated solid generation, database storage of historical results and comprehensive compliance reporting.
Inputs include: the mine plan (planned surface at the beginning and end of period OR planned solids); the actual surface (at the beginning and end of period); and the stage limits (polygons).
The mine plans (movements and grades per stage/period) can be imported into an SQL database from Maptek Evolution, or in a standardised .csv format. Factors such as budget, forecast, short term planning and stripping can be included and there is no limitation on the number of plans that can be stored.
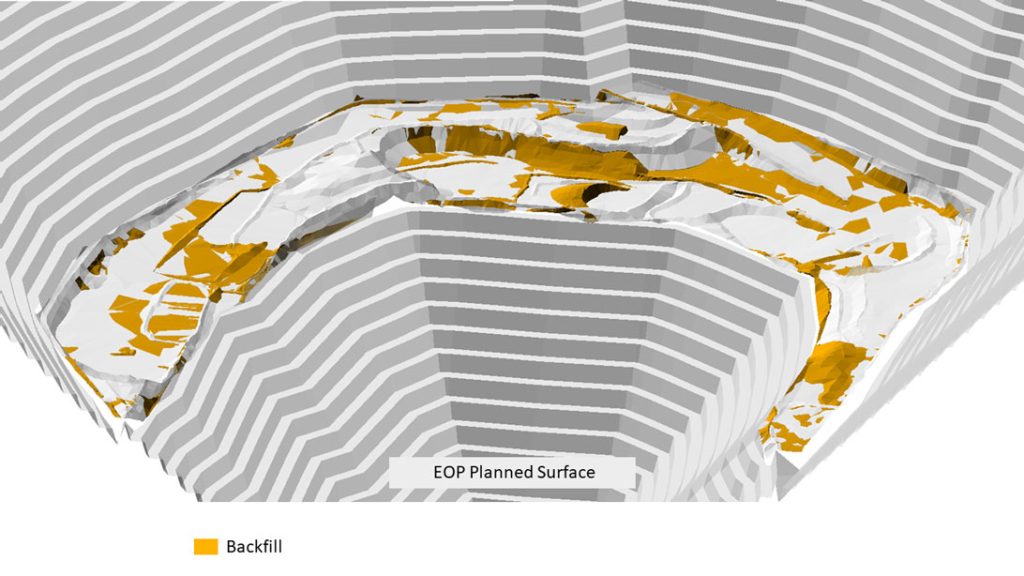
The output intersection solids are created directly from the surfaces and/or planned solids. The user must validate those intersections, cropping or removing solids according to criteria based on their expertise.
The solution sees a surface intersection performed every time a period is analysed. A period can be years, months, weeks or any unit defined by the user.
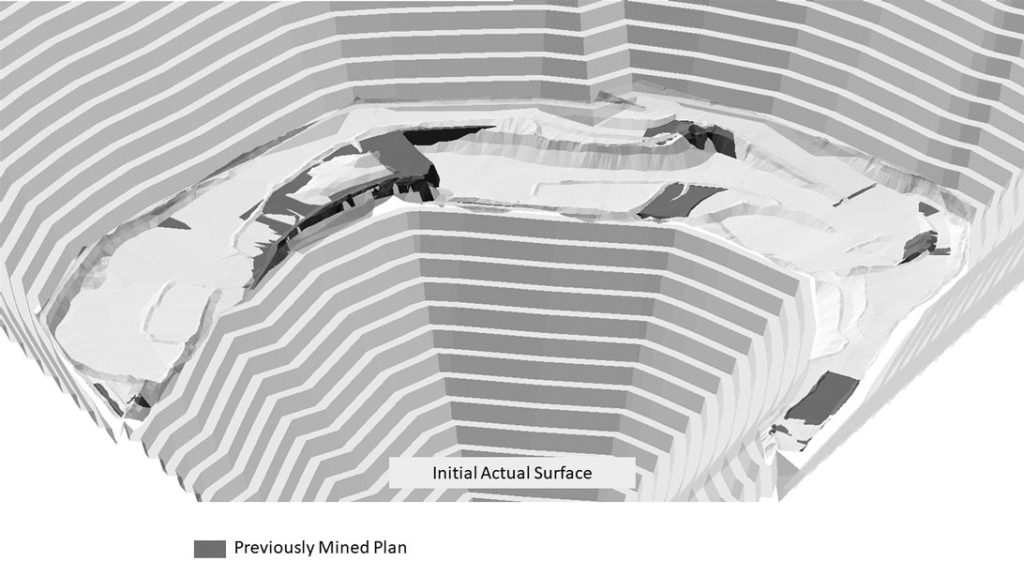
The validated solids showing mined and not-mined volumes as well as reserves calculated from the block model, are stored in the SQL database.
The stored data is associated with one of the plans already loaded in the database, including volume, tonnage and grade. The data can be used on a web application or PowerBI dashboard.
Compliance reports are output from the SQL database for any period analysed, and with respect to any desired category.
This can include: monthly volumes, spatial and volumetric compliance; year to date plans with month by month movements, ore/waste product breakdown, and monthly deviation from plan with regard to volumes and grades.
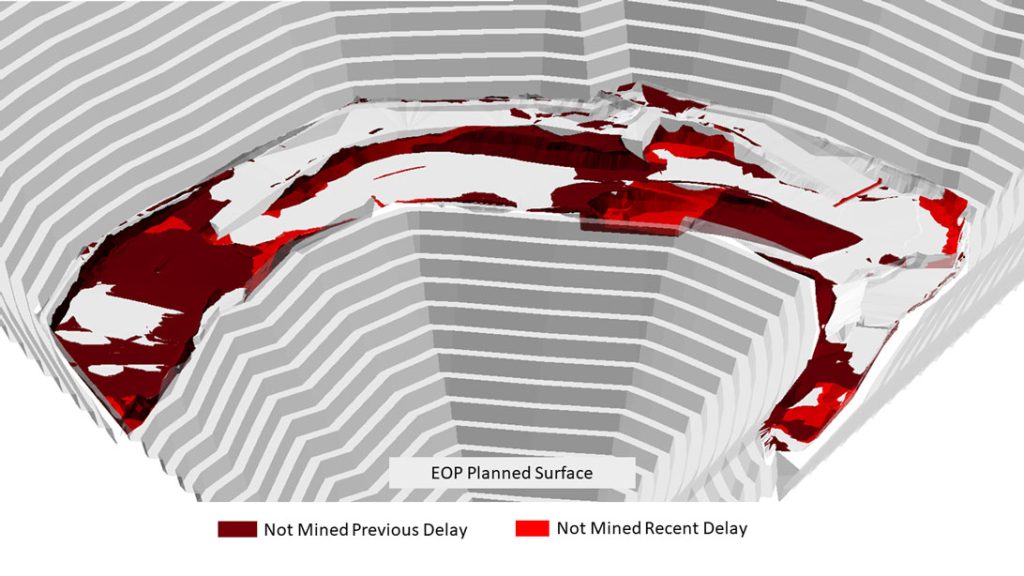
This automated approach provides planning engineers with a robust tool for plan conformance analysis on a monthly, weekly or daily basis. Engineers can now spend more of their time analysing results and making timely decisions to prevent further deviations.
Maptek can tailor this solution to your operational requirements.
- With unplanned work costing 1.5 to 5 times more than planned work, mine budgets can soon blow out
- Comparing historical data to plans across weekly, monthly, end of period and yearly planning horizons delivers timely decision support
- An automated approach to measuring mine compliance provides a robust engineering tool for analysing conformance and improving adherence to plan